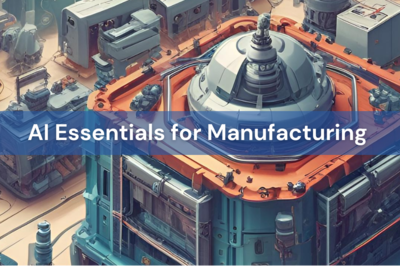
By Andrew Montgomery
Introduction
Few technological advances have generated as much excitement as artificial intelligence (AI). None more so than generative AI. Manufacturers view AI as integral to the creation of hyper-automated and intelligent factories. AI is seen as a powerful tool for product and process innovation. It reduces cycle time, minimizes waste, improves maintenance practices, and enhances demand, inventory, and forecasting capabilities — all while contributing to achieving sustainability goals.
In an industry study by MIT Technology Review Insights, researchers interviewed 300 manufacturers that have begun working with AI. Most of these (64%) are still in the early phases, currently researching or experimenting with AI. 35% of executives indicated that they have begun to put AI use cases into production.
To thrive in today’s dynamic market, manufacturers must leverage AI by developing and scaling use cases. To facilitate this, manufacturers must also address challenges with talents, skills, and data.
We will explore these essential areas of opportunity, critical obstacles for information technology (IT) and operational technology (OT), and techniques to scale AI in manufacturing.

AI’s Triple Threat: Boosting Design, Efficiency, and Sustainability
Companies that successfully implement AI-powered solutions have already seen significant reductions in downtime and improvements in labor productivity. A McKinsey study shows manufacturers that have adopted AI practices have reported cost decreases by as much as 55%, and revenue increases by 66%. Improvements were realized in these three areas of opportunity: product design and development, manufacturing productivity, and sustainability.
Product Design and Development: Manufacturers can revolutionize product development by accelerating design processes, enhancing innovation, and improving overall efficiency.
- Design Twinning: Digital twins of in-development products can be evaluated, tested, and rapidly iterated long before the first prototypes are constructed.
- Customization: AI allows for greater customization in production, enabling manufacturers to meet specific customer needs more precisely and efficiently.
- Solution Development: AI solutions can be integrated into the product, unlocking new capabilities that interpret and respond to complex signals that traditional software rules or logic cannot handle (e.g. object recognition).
Manufacturing Productivity: Manufacturers have a substantial opportunity to transform operations as AI becomes more accessible — from optimizing resources to eliminating waste, and improving throughput. Here are several key areas where AI can drive significant improvements:
- Predictive Maintenance: By taking historical data from maintenance logs, you can predict how a machine will behave under a future payload, whether you’ll need to fix it, when, why, and how — based on what fixed that problem in the past. This can reduce downtime significantly.
- Predictive Quality: Predicting and reducing failures can yield significant cost savings.
- Waste Reduction: Using metrics to predict behavior across product specifications and processes can minimize scrap and maximize product quality.
- Demand/Inventory Forecasting: With a thorough understanding of plant operations and the data behind production, it’s possible to forecast the demand and movement of critical parts, resulting in significant inventory savings.
Sustainability: Manufacturers have a responsibility to balance economic growth while also minimizing their impact on the environment and society. AI can help manufacturers improve supply chain transparency, enable them to design and produce more sustainable products, and minimize environmental impacts.
- Energy Utilization: Using metrics and historical trends we can predict energy demands and optimize factory operations to utilize more environment-friendly energy as well as reduce waste.
- CO2 Emissions: Real-time monitoring of emissions throughout the manufacturing process can identify and address emission hotspots promptly.

Bridging the Gaps: Overcoming Challenges to AI Adoption in Manufacturing
Manufacturing is undergoing a revolution, with traditional boundaries between operational and technological teams dissolving. AI and its associated advancements are a catalyst, pushing collaboration to the forefront. Let’s unpack five critical challenges that IT and OT must tackle together to harness the full potential of this transformative era.
- Data, Data, Data: Data quality, weak integration, and data governance are the most commonly cited reasons for project failure and use case abandonment. In the MIT research, 57% of executives cited data quality hampered use case development.
- Talents and Skills: A lack of talent and skills is the toughest challenge in scaling AI use cases. The closer use cases get to production, the larger the impact. Additionally, data quality and governance as well as insufficient access to cloud resources are magnified due to workforce gaps.
- Stakeholder Alignment: Adopting AI in manufacturing involves significant changes in processes, technologies, and mindsets. It is crucial to ensure that these changes are successfully implemented in a sustainable way.
- Fragmentation: Most manufacturers find some modernization of data architecture, infrastructure, and processes are needed to support AI, along with other technology and business priorities. Modernizing data systems to improve interoperability between engineering, design, the factory floor, OT, and IT is a critical priority.
- Use case definition: Identifying the right use case is essential to AI adoption. Manufacturing systems are holistic and one metric has implications for multiple downstream systems. Additionally, it is easy to fall into the trap of never-ending analysis. Selecting the right use case and clearly identifying its dependencies is critical.

Building a Sustainable AI Foundation: Strategies for Success in Manufacturing
There can be a lot of skepticism about introducing AI solutions in manufacturing and whether the investment is justified. To overcome hesitancy and create trust with AI-powered solutions, you have to: 1) Be Intentional about the use case that is developed, 2) Assemble the right team (including leadership, operations, IT/tech, digital transformation, and finance people), and 3) Adopt a data first agile delivery process that reflects data accessibility and feasibility with model development.
Below are 5 techniques we have found successful in supporting these needs and ensuring we can unlock the power of AI in manufacturing:
- Getting the right people in the room: AI is not just an IT or data scientist’s problem. AI is an integral part of solving complex business objectives and as such requires a multidisciplinary team to unlock it. It requires OT leaders, IT leaders, finance leaders, and SMEs to work together to design and plan solutions. This approach ensures there is both top-down and bottom-up support, that the appropriate budget is allocated relative to the target ROI, and that the right skills are available to execute.
- Starting small and achievable: There are so many things that can become hurdles in implementing AI in manufacturing, from overcoming incompatibilities in systems to securely connecting shop floor systems and networks to the appropriate cloud systems needed to build and run AI models. Prioritizing a well-defined, value-adding AI use case within a single facility can cultivate internal advocates for AI. This initial success can then be leveraged to build a collaborative foundation for future AI initiatives.
- Gaining consensus on how to track progress: Aligning the organization and team with what “done” means and the mechanics that track progress is critical. Oftentimes, organizations struggle to align the IT, OT and business stakeholders. That is why it is critical, given the dynamics of delivering AI solutions into always-on manufacturing environments, that an end-to-end lifecycle be represented in milestones and iterative success criteria. This allows the delivery, deployment, and operational teams to understand their target metrics, and stakeholders understand the progress through the lifecycle of the project.
- Quickly identifying and understanding data gaps: It is important to realize that what looks good with simulated data may not be achievable in practice for many reasons. Commonly identified issues include system interoperability, data quality, and data governance. It is critical to understand gaps and mitigation strategies early while evaluating and prioritizing use cases to develop. Stakeholder support can be lost if you experience too many false starts.
- Clearly articulating foundational and use case investment: Whether this is the first use case being developed or the use cases require integration with older OT systems, there is likely a need for some incremental investment into foundational systems and architecture.
It is important to clearly understand this investment independent of the use case(s) being developed, because the funding and ROI may match different time horizons. With this in mind, programs manage these deliverables as separate work streams with different ROI horizons.
To realize the value of AI within manufacturing, organizations must comprehend use case feasibility, address gaps early, and adopt a delivery methodology that can align and deliver.
If you’re looking to leverage AI for your organization, our team can partner with you to unlock value and mitigate pitfalls. Learn about our AI and data insights expertise and workshops, and be sure to follow us on Medium for upcoming content.
Sources:
Taking AI to the Next Level in Manufacturing, MIT Technology
State of AI in 2023, McKinsey Study
Andrew Montgomery, vice president of strategy, is an experienced technology executive and data strategist with 20+ years of experience with Fortune 500 companies. Andy’s focus is helping customers unlock their data to simplify business complexities and reshape business outcomes.